Since the delivery of the first jet in 2012, the United Kingdom F-35 programme has expanded tremendously.
Recently, the UK fleet reached a new milestone, when it crossed the threshold of 10,000 flight hours.
This milestone has been nearly 10 years in the making.
In 2012, the first F-35B was delivered to the UK. Currently 21 of the planned first batch of 48 aircraft designated for the Royal Air Force and the Royal Navy are operating as three squadrons in two locations: the 617 ‘Dambusters’ Squadron and 207 Operational Conversion Unit Squadron at Royal Air Force Marham and the 17R Test and Evaluation Squadron at Edwards Air Force Base, California.
From the moment the first F-35 was delivered to the UK to the fleet’s most recent achievements, the UK F-35 programme has driven collaboration among global allies, cementing itself as a cornerstone of coalition operations say Lockheed.
Here’s a look back at some of the programme’s most significant milestones over the years.
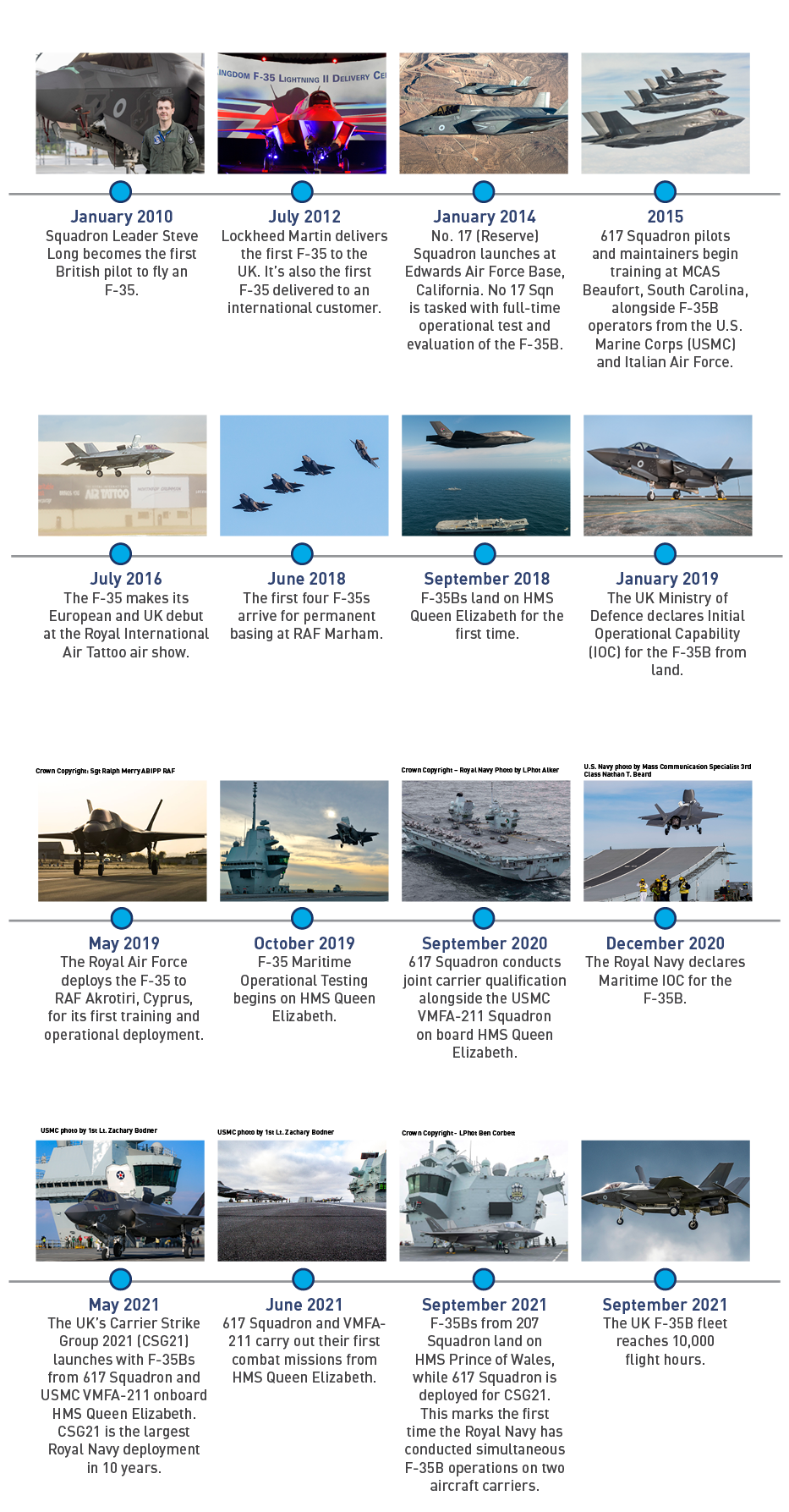
Fantastic news.
Any updates on what engine will replace the current version going forward to keep it ahead of the competition and future updates?
The Pentagon is exploring its options for a more efficient and powerful F-35 engine
https://www.defensenews.com/air/2021/08/12/the-pentagon-is-exploring-its-options-for-a-more-efficient-and-powerful-f-35-engine/
And for those who fail to keep an eye on the ball.
If you need the actual report, let me know!
GAO Warns of Ballooning F-35 Sustainment Costs, Need for Plan to Cut Billions
https://www.military.com/daily-news/2021/07/08/gao-warns-of-ballooning-f-35-sustainment-costs-need-plan-cut-billions.html
Unfortunately, they have no intention of handicapping the new generation GE engine by making it compatible with STOVL operation.
The F35B will continue with the current engine, perhaps with some light modification.
The B model appeared to be a bit of a developmental dead end unfortunately…
All 3 variants of the F35 are very much at the beginning of it’s growth cycle. In 10 years, it will be a very different capability to today. Including it’s engine. The F135 has considerable growth potential in both terms of thurst, and electrical power generation.
We can hope Robert, unfortunately when the half British F136 was cancelled, we lost any real input into F35 propulsion.
Further development of the F135 is tied to the progress of the new GE lump. ‘If’ that powerplant moves into production for the A and C model, and is retrospectively fitted to earlier jets, then funding any serous upgrade package for the F135 will become a political football and probably starved of funding.
I can see the B model being progressively sidelined, I think as sales of the A model progressively build, Lockheed Martin would be quite happy to simplify its life and stop B production by 2030, though hopefully the avionic upgrades will keep pace with the A and C fleet into the 2040’s.
We will see I guess, I just have a feeling the overly complex nature of the B model has caused massive programme headaches from the start and increased the cost for all three variants, once the core USMC order is complete, its only going to be dribs and drabs from niche operators like the RN and the Italians …
Hi John. Yes, it was a shame the F136 wasn’t continued. Lots of question marks about the AETP project, and so far a requirement to install the engine on F35 doesn’t exist. But it could potentially happen. I think you will see this new engine on whatever the new 6th gen platform will look like. Fascinating tech though.
China may have reverse engineered it by then, so maybe…
Well not reverse engineered, but rather copied from plans they have stolen, is what I should have said!
Handy for top up orders!
I see so the US will then clearly signal “buy the version of our plane that works for you then we can it”.
Have I summarised that right?
Would the UK, Italians, Japanese, South Koreans and Taiwan be a bit miffed about that. Not really alliance building stuff, is it?
So all this F35B dead end stuff doom is a bit wide of the mark.
F35B is what will equip all of the US’s allies carriers for a long time so it is an essential part of the alliance project mix. And unless USMC are given something else pretty essential there too.
In a strange way I see the B version as being more likely to outlive the A & C versions as it fills a unique niche. The A version will be supplanted by 6th Gen quite soon: no doubt about that assuming the glacial rate of the pork barrel is overcome.
Why cannot RR build a power plant for the F35B. There would be a market and it may be better…
They were working on the F136 Engine with GE until Developement was stopped in 2011.
I am sure they could Rob, RR is perfectly capable of designing a significantly more capable engine, the only trouble is it would radically increase the unit cost beyond economic viability.
The USA wouldn’t be able to screw money out of it.
Agreed, the only interest in C is from the USN… and they seem to have reversed policy and are ordering more 4th generation aircraft. I think the A and B will prove to be the longest-living variants.
They are only ordering new super hornets of the latest type to replace legacy hornets. This is because all the F35 for several years are spoken for, they need to replace all the old hornets pretty damn soon with the hours on them so they are taking as many F35c as they can while replacing old 4 gen with 4.5gen.
Morning SB,
Hey, its just my interpretation of the programme as it stands.
By the time the USMC have taken delivery of the final aircraft and the next largest user, the UK, will probably be finishing up about the same time in the 2030 timescale.
Orders will tail off, unless their is another substantial ‘B’ order (50 plus), then I think its about done.
The cost of ordering B specific items in small numbers, lift fan etc, will go through the roof, thus will the unit price.
Perhaps there will be substantial orders forthcoming, who knows with ever changing situation in the Far East…
However, its my take on this that LM will concentrate efforts on updating the A model, to keep it relevant at a time when Gen6 is emerging onto the market.
They will probably take the F16 ‘growth’ approach, slim the product line to an advanced F35D/E variant, incorporate a new engine, avionics and weapon systems and try to keep the orders coming in and the cost point down.
Substantial orders from the USAF will probably make this possible as it adjusts to a high end Gen6 and low end F35 variant as its force mix for 2040.
Just my opinion on how I see the F35 market develop over the next 20 years, over options are of coarse available… 😄
This is what the USMC are now saying, as well as putting 35bs on Assult class and every allies heli carrier increases air power.
Not so sure, the B still shares a lot of architecture with the A & C so to some extend the B will get free carry off the back of lagre A and C orders. And there’s already around 450 Bs ordered so we’re probably looking at 500+ longer term, as many Bs approx as Typhoon, Gripens, Rafale’s etc and they get upgrades.
Don’t forget South Korea and Japan. Now that Australia have woken up to the threat of Chinese expansionism. Would they relook at the F35B for the Canberra class?
The problem with the F135 growth engine is that it apparently wont fit the airframe of the B model. Which possibly means that its grown in diameter. Perhaps RR and GE should look at reinvigorating the F136? It had better potential growth than the F135. There’s definitely a market for an improved engine for the F35B.
Hi mate,
The issue as I see it is one of large scale orders, if B production drops to a trickle, 12 here, 24 there, then the unit cost of the B will become unaffordable. It’s only really viable at the moment while there are hundreds of them under regular multi year contracts for the USMC.
Volume production, drops the unit cost of the lift fan and the many other B specific items.
As we all know, in reality, the B has little construction commonality with the A and C, requiring many bespoke and production adjusted components.
When USMC production is concluded, there will be a sharp (and very considerable) rise in the unit cost of the B, probably rendering it beyond the reach of most countries finances.
We best make sure we have our 80 ‘ish’ under contract before the USMC wind down orders.
I agree. P&W will if they use the growth engine, effectively create two separate engines for the F35 anyway. So if there are only say 300 F35Bs with the standard F135 plus a few spares. I still think it would be doable for a new non P&W improved engine.
With the progressive movement of the B model onto the USN assault class ships, increases the USN flat tops by 6 carriers, and means the USMC are more active with the upgrade of the 35Bs over the AV8Bs .
And with the 35bs being looked at by most of the Nato partners to put aircover on a Heli-carrier.
the feeling in Lockhead is the B could become the better option.
its all over the USMC news….
potential 35b sales Japan/Australia/Korea/UK/Italy/ Singerpore/
Anyone with a heli-carrier is now looking @ Bs as an option to provide air cover to there fleets.
but could all change at any point.
Yes, and they need to as its got its issues. something like 1/4 of US jets are waiting for engines issues to be resolved. Funny commercial airlines have given RR and P&W hard time on engine issue military need to take leaf out of civil aviation’s book imo.
This concerns me even more. Worth reading in full. as it is factual rather than based on one individual’s opinion!
First flown 11 June 2008. It will be approaching 20yrs before it can deliver what was promised on the lid if all goes to plan.
With 6th Gen aircraft already in development, you begin to see the dilemma facing the powers that be!
I’m guessing minimal orders of the F-35B complemented by Vixen due in 2023 (first flight trials), hence the request to industry for EMALS within the same timeframe?
“Static Structural and Durability Testing Activity •
• Teardown inspections of the original F-35B full-scale durability test article (BH-1) completed in October 2018.
The program canceled third lifetime testing of BH-1 due to the significant amount of discoveries, modifications, and repairs to bulkheads and other structures that caused the F-35B test article to no longer be representative of the wing-carry-through structure in-production aircraft.
Release of the DADT report on BH-1 was expected in November 2020, but has been delayed to 2021.
The program secured funding and contracted to procure another F-35B ground test article, designated BH-2, which will have a redesigned wing‑carry-through structure that is production‑representative of Lot 9 and later F-35B aircraft.
Contract actions for BH-2 were completed in November 2019 and testing of the first lifetime is scheduled to begin in 1QFY24. The BH-2 ground test article will come from Lot 15 production.
• Disassembly and teardown of the F-35C durability test article (CJ-1) completed in November 2019. The program stopped testing during the third lifetime testing in April 2018, following the discovery of more cracking in the Fuselage Station (FS) 518 Fairing Support Frame.
The cracking was discovered near the end of the second lifetime and required repairs before additional testing could proceed.
After estimating the cost and time to repair or replace the FS 518 Fairing Support Frame, coupled with other structural parts (i.e., fuel floor segment, bulkheads FS 450, FS 496, FS 556, and front spar repair) that had existing damage, the program determined that the third-lifetime testing would be discontinued.”
Release of the DADT report on CJ-1 was expected in November 2020, but has been delayed to 2021.
Cracking is not totally unexpected as structural analysis software is not 100%. If we looked at a RAF Chinook such as ZA718 “BN”. This aircraft has seen about 40 years of service and has been constantly upgraded. The aircraft is a model C Chinook. This used frames that were built up from a number of parts, rather than the later D and F model Chinooks that use one piece frames milled from solid. This means that as the airframes flexes from picking up and dropping loads over time these cause fatigue cracks such as from drilled rivet holes. But it also causes tears in frames.
Depending on the location and direction of the tear/crack, it can be deferred for repair and just monitored. If the tear/crack gets longer than a red line limit, the frame will need repairing. This can be done through either plating over the crack, where the plate then takes the load away from the torn/cracked frame or depending on time constraints replace the whole frame. All the first batch of Chinooks have some form of plated repair to their frames, especially following Afghan.
The newer Model D and F Chinooks with their milled frames are stiffer, so don’t flex as much. However, they still tear and crack but in different locations as the resonance nodes have moved to new locations.
This will be similar to the F35. Each model (A, B and C) will have a different resonance and therefore show up different areas where cracking appears. These areas will have been mapped and monitored on the early Block 1 models. Then improvements to frame shapes, materials and thicknesses done to the later Block models from lessons learnt. The process will be continuous throughout the aircraft’s life.
Have you read the report? I can’t locate it? Would you be kind enough to post the link! BH-2 will not begin until 2024 at the earliest it seems.
“Release of the DADT report on BH-1 was expected in November 2020, but has been delayed to 2021.”
“The program canceled third lifetime testing of BH-1 due to the significant amount of discoveries, modifications, and repairs to bulkheads and other structures that caused the F-35B test article to no longer be representative of the wing-carry-through structure in-production aircraft.”
“Contract actions for BH-2 were completed in November 2019 and testing of the first lifetime is scheduled to begin in 1QFY24. The BH-2 ground test article will come from Lot 15 production.”
No, I have not seen the report. But what I can gather is that the very early Block F35s are now no longer relevant as test mules, because the later versions of the F35 have moved on significantly structurally.
Great News ……………… although the build-up of the F-35B fleet remains glacial (although that didn’t stop the MoD chopping Tornado earlier than its original planned OSD of 2025 !)
For comparative purposes:
Between 2003 – 2014 (11 years), the RAF Typhoon fleet racked-up 100, 000 flying hours.
Between 2012 – 2021 (9 years), our F-35B fleet has achieved only 10, 000 hours.
These figures do illustrate how critical a mere seven front-line squadrons of Typhoons are to UK combat-jet operations.
Would the RAF not have had considerably more Typhoons during that time compared to F-35 numbers, making that comparison slightly warped.
Don’t get me wrong F-35 buy rate is slow for various reasons, but from what I know the RAF would have had at least double if not triple the numbers of Typhoons during that period compared to the number of F-35s the RAF have now.
Please do correct me if I am wrong.
Hi Wilhelm, I’m not in a position to correct anyone! lol
But for me, I think the figure reinforces how REALLY slow the F-35B build-up has been. Certainly in marked comparison with the Typhoon force (and indeed, when looking at the introduction of Tornado during the 1980s).
Agreed – there are reasons: political, financial – and technical.
But taking those into account, the force build-up still seems markedly glacial.
A slow build-up does put a lot of pressure on those seven Typhoon squadrons – due to drop to only five squadrons in 2025.
Another part of the equation is that due to the high operating costs of F35, still not down to levels promised/envisaged, the MOD have reduced their flying hours to compensate. Not sure by now many per year, but they do less then Typhoons.
So you want us to buy all the planes for the next 20 years in 1 go, on an early software level that cant do half of what we need and costs a fortune to upgrade in 5 years and still has issues on it?
This is how all military planes are bought. You do not buy all tranche 1, you buy constantly through its life ie: typhoon and how we are retiring tranche 1 that are very limited in capability
Hi andy, No – I don’t want the UK to buy the F-35B in one go – that would be a wee bit daft!
But I do think the force build-up is rather too slow, putting pressure on other assets. Or to mitigate the wait for Block 4 aircraft – the MoD should have run Tornado out to 2025.
That’s all I’m stating – and it’s hardly controversial.
Just to recap –
One of the reasons for the glacial production numbers is that Turkey was thrown out of the project, which has knock on effects for the rest of the production. As these items would have to manufactured else where within the “F35 team”. In some regards, it might have been better if the UK had arranged to build F35s in the UK, probably from kits.
One reason for the slow production rate, plus engine parts being manufactured in Turkey.
In the meantime, the Air Force is slowing its F-35 buys, calling for 48 in fiscal 2022 then 43 per year from fiscal 2023 to fiscal 2026, a 10 percent drop from its previous future years defense plan.
https://www.airforcemag.com/kendall-current-f-35-block-4-issues-earlier-jsf-problems/
Ten thousand flight hour for the UK fleet? Pretty good.
And despite all the negativity from the F-35 haters, the global fleet has set some pretty goals, as a 1 October 2022:
https://www.f35.com/content/dam/lockheed-martin/aero/f35/documents/F35FastFacts10_2021.pdf
* 705+ aircraft delivered
* 443,000 flight hours
* 1485+ pilots trained
* 11,220+ maintainers trained
* 251,425 sorties
Cheers,
Hi folks hope all is well.
Good news and makes us proud of our military, however, I’m a bit confused about this number. “Currently 21 of the planned 138 aircraft designated”.
I’m not too sure if this number will be reached? Realistically 75/80 maybe.
Cheers,
George
I was thinking the same, last I heard, the MoD had flatly states that the full 138 jet order will not be met
I missed that. I thought they were still playing it smart and being non-committal. Can you remember where/when you heard it?
Just refreshing my memory and it looks like it was only speculation. Lots of reports on a reduced order from Feb/March this year but nothing confirmed. False alarm!
Sure I remember reading one of the Chiefs suggested in a speech earlier in the year, that the final number of airframes would be in the 70-90 range.
In fact, I am sure it was referenced in an article on here.
In fact, here’s a link to the UKDJ article, which contains a reference and a link that you might be interested in having a look at.
https://ukdefencejournal.org.uk/uk-confirms-plans-to-order-more-f-35-jets/
Hi Jon. I heard a similar revised number from the MOD in the last review, circa 80 -90.No firm timelines or definite numbers though!
Hi George, Hope this article enlightens you as to the prospect of further deliveries. Block 4 is pushed back until 2027 if all goes to plan!
23.06
LONDON — The high costs of supporting F-35s and a failure to quickly integrate the MBDA Meteor missile to the aircraft could slow British plans to buy more of the jets, defence secretary Ben Wallace warned June 23.
“Wallace told Britain’s Parliamentary defence select committee that he had the budget to buy more than the 48 jets the military has already ordered but wanted to see progress controlling maintenance costs and fair treatment for integrating Meteor.”
https://www.defensenews.com/global/europe/2021/06/23/two-reasons-britain-could-slow-its-purchase-of-the-f-35/
I have a F35B question, slightly off topic. Why did the American’s decide on a lift fan engine as opposed to the swivel thrust nozzles in the Harrier? Surely this would be far more cost efficient and simpler to maintain?
Operationally, this would mend a significant weight saving, extending range and payload. I get that the F35B is way heavier than the Harrier, but part of this is self imposed by the lift fan and dead weight in conventional flight
Anyone have insight on this?
Great question Klonkie. If they had swivel type configuration would it then have been possible to have a twin engined F35B?
Does any know if there’s an option for the UK to have a more developmental lead into an updated F35B down the track?Both hardware and software and building on the Meteor and Spear integration.
I’m afraid not. Lockheed Martin have proprietary rights over the whole F35 program. Which means the UK would have to make a settlement with them to do anything that comes outside the scope of the program. This would also be the same for a new engine, as only the F135 and F136 were certified. A new engine would need a whole host of ground and flight trials.
When the F35 was being designed im sure the Harrier would have been studied extensively,as was the Yak 141,so logically the end result must have been a system that offered a vast improvement rather than stick with what was done before.
agree, think the uk were thinking to follow up on the harrier but saw that the American F35 proposal was a logical design and useless to go into competition with the yanks. correct me if i am wrong.
BAe had a separate VTOL proposal prior to the F35 program in the 1980’s. with their P1216 prototype. It was going to be a direct replacement for the Harrier and Sea Harrier. It was going to use a new 3 poster turbofan engine, that would have incorporated an afterburner, as well as the plenum chamber burners for the cold air nozzles. It certainly would not have been a stealthy aircraft, but would have been unsurpassed in aerial dogfighting. BAe had planned to incorporate “viffing” into the flight control software as a “normal” manoeuvre.
When the first F35 test mules were flown, they had pretty constrained flight control software. However, one of these aircraft had it relaxed too much, and a US test pilot tried to slow the aircraft down rapidly in a pseudo viff manoeuvre. The result was most of doors over and below the lift fan got ripped off and subsequently damaged one of the vertical stabilisers.
It was all to do with the centre of balance/gravity in the hover and the requirement to go supersonic. If you look at a Harrier, you will notice how short it is in length. With the Pegasus engine you need to place the four exhaust plumes near the centre of gravity. This then has a knock on effect on how the exhausts are routed through the airframe. For example long large diameter hollow pipes will take up a lot of volume, that could have been used for fuel. It also significantly complicates incorporating an afterburner, as this will now need to be split into two pairs. Plus the afterburner won’t be massively effective, as the majority of the unburnt bypass air is pushed out the forward two nozzles. Without an afterburner the aircraft cannot achieve sustained supersonic speeds in level flight (not to mention the fixed open intakes).
The Yak 141, solved this by using a single low bypass turbofan whose exhaust swivelled down through 90 degrees and balanced it with a pair of vertically mounted turbojets. This meant it was much easier to incorporate an afterburner. Also it allowed the engine to be placed much further back, thereby allowing more room for fuel. The two vertical engines were seen as the simplest solution, as it meant the airframe could be narrower, rather than accommodating a single larger diameter engine. However, if one failed the aircraft could no longer hover. It also meant that in a hover the aircraft eats through fuel.
The F35 uses a similar concept to the Yak 141. By placing the engine further aft and using a rotating nozzle you create space for fuel. Perhaps more importantly though it simplifies incorporating an after burner, thereby allowing supersonic flight. But this has to be balanced by having a lift device in front of the centre of gravity. The BAe lift fan is an elegant solution to this problem. The fan’s drive train and clutch can be isolated in forward flight to remove any parasitic drag from the engine. But in the hover, the large diameter fan produces significantly more thrust that the two vertically mounted jet engines in the Yak 141 and still eats not as much fuel. The main issue is that the horizontally mounted fan takes up a large volume, which on the A and C model is used as a fuel tank. It also makes the airframe wider so increases drag, hence why the B model is slower than the other two. To balance the aircraft, it also has a pair of roll jets exiting under the wing inboard of the first hardpoint position. Yaw is controlled via the rear swivelling nozzle, thus removing the need for reaction jets and their ducting as per a Harrier.
Unfortunately, there is no other simple way of creating a supersonic VTOL/STOVL aircraft. We could at some point replace the lift fan’s drive train and clutch with an electric motor driven fan, to save some weight. Or you could use a much higher bypass ratio turbo fan engine, where the majority of the bypass air was then fed forward to a nozzle arrangement in front of the centre of gravity. But then that comes at the cot of using up space that could have been used for fuel by the ducting. Until Tony Stark’s repulsor technology become fact rather than fiction, we are stuck with making compromises.
Wonder if possible to fitted the front end of a Pegasus engine (cold fan) to the rear of the -135 engine with single swivel nossle (with afterburner) even if that was enbedded deeper (would help mask IR) as front swivel up/back they feed through fuselage to rear nossle giving more normal flight thrust? can you have longer gap between compressor stages things like that? with long drive shaft (like lift fan in front of -135) vents on top during hover for airflow which is replaced by flow from front nossles as they rotate up
I think you are trying to describe a dual cycle engine. This was proposed in the late 1980’s, where a turbojet had a drive shaft mounted to the front of it, that then drove a large diameter fan. This was supposed to be used during take-offs and climbing. Where the increased bypass flow would help to increase the thrust but also reduce the noise. When the aircraft reached a certain height the fan was de-clutched and the air intake closed. The aircraft was then totally powered by a turbojet fed by a separate air intake.
This concept then developed into the variable cycle engine. This is where you combine the attributes of both a turbofan and turbojet in one compact unit. It is done by using a turbofan with a bypass ratio greater than 1.5. Normally, the bypass air passes over and around the rest of the engine and then passes out through the one exhaust. As the aircraft flies higher, the bypass air is diverted into the core of the engine helping to offset the reduced amount of oxygen, until all the air is diverted through the engine turning it into a turbojet. The GE/RR F136 was a partial variable cycle engine, where only a portion of air was diverted into the core of the engine.
The F135 has a higher than average bypass ratio for a fighter engine. There are number of reasons for this, but one of the reasons is stealth. It uses this larger flow of colder bypass air to cool the hot air that is exhausted from the engine, thus lowering the plumes heat signature. It also means the afterburner is a lot more powerful, as there’s more fresh air to use.
Placing a fan in the exhaust stream is not a good idea. For starters it will need to be sufficiently cooled so that it does not become a hot spot, visible from the back of the engine, especially when the afterburner is being used. If it is being spun by the engine, the drive shaft and the fan itself will cause a parasitic drag on the engine, making it slower to accelerate. If the fan is powered purely by the exhaust gas flow and not mechanically, it will rob some of the thrust.
Saab’s JAS 37 Viggen incorporated a neat design with its thrust reverser. The thrust reverser was held in a circular shroud that enveloped the variable diameter exhaust nozzle. However, where it met the rear of the airframe, large slots were cut into it. This had the affect of diverting the airflow around the tail, through the slots so that they mixed with the exhaust plume and thus lowered the IR signature. I am surprised they didn’t carry this forward for the Gripen?
Thanks, just dumb laymen thinking that it wouldn’t be to ‘hard’ to take cold Fan front of the Pegasus disconnect it put long shaft (between compressor and turbine) back to the rear hot bit with swivel down nossle (to spread lift) would need 2 ducts to route air from front nossles when in forward flight through to rear) and out, I was under impression the on pegasus front nossle pair were cold and the rear pair were hot (needing water injection during hover) so wondered if could make those in to single exhaust like -135 also then giving afterburner (go fast)
That’s pretty much the variable cycle engine. The engine would have to use a much larger bypass ratio, so there is enough mass airflow (slower colder air) to balance the aircraft. The issue you would have is the plumbing for the cold air nozzles, where they would need to go over the aircraft’s centre of gravity, to rebalance the aircraft in the hover. It’s definitely doable, but you will have to take the hit of the large diameter pipes, using up volume that would have been used for fuel. The cold air nozzles could be fixed facing downwards with deflectors to change the airflow direction, which would be better for a stealthy aircraft. Or like the Harrier use swiveling nozzles. It may even be feasible to use plenum chamber burning to give you more thrust in the hover.
Many thanks Davey- detailed and thorough explanation. I had thought the the tail swivel exhaust could balance the four fuselage swivels- positioned to where the lift fan currently sits. This is however all well above my pay grade.
Actually 21 aircraft is an old number, c. July. The 24th UK F-35B aircraft first flew on 2 September 2021 and is now assigned to 207 Sqd RAF. The 25th aircraft is also complete but not yet delivered, and two more are in build – so we should have just about enough Lightening’s to reform 809 NAS as planned next year (1 April?) with “up to” 8 aircraft nominally on strength. But long held (2015?) plans to have 35 F-35B’s by the end of 2022 and 48 by the end of 2025 have recently slipped by a year or two.
Also, if my memory is correct the first three UK aircraft (delivered 2012-2013) can’t be upgraded to an operational standard – currently Block 3i for UK aircraft, but the USMC is now rolling out Block 4 upgrades. Indeed the first two UK aircraft are wired and configured as development, test and eval aircraft. I expect that they will be quietly pensioned off in a few years as being too out of date, too expensive to maintain, and no longer useful even for training purposes.
The MOD refused last year to answer a PQ asking how many “early model” UK F-35Bs will eventually be upgraded to the Block 4 standard, declaring that it will decide numbers based on “military capability requirements”. Presumably the next UK order will be for new build Block 4 aircraft, but UK MOD and Ministerial announcements are nearly meaningless in this regard. What matters is a US DOD announcement that a contract has been agreed with Lockheed Martin that includes X number of aircraft for the UK.
“What matters is a US DOD announcement that a contract has been agreed with Lockheed Martin that includes X number of aircraft for the UK.”
That has nothing to do with the US DOD.
Does anyone know how many planes we will get above the initial 48? Also when does the first FAA unit come on line?
TBC in future Defence Reviews i believe,as for 809 NAS wiki says it will stand up in 2023.
The last sea lord I believe said they were aiming for about 100 but over the program life
138.